6 Tips for Spare Parts Management
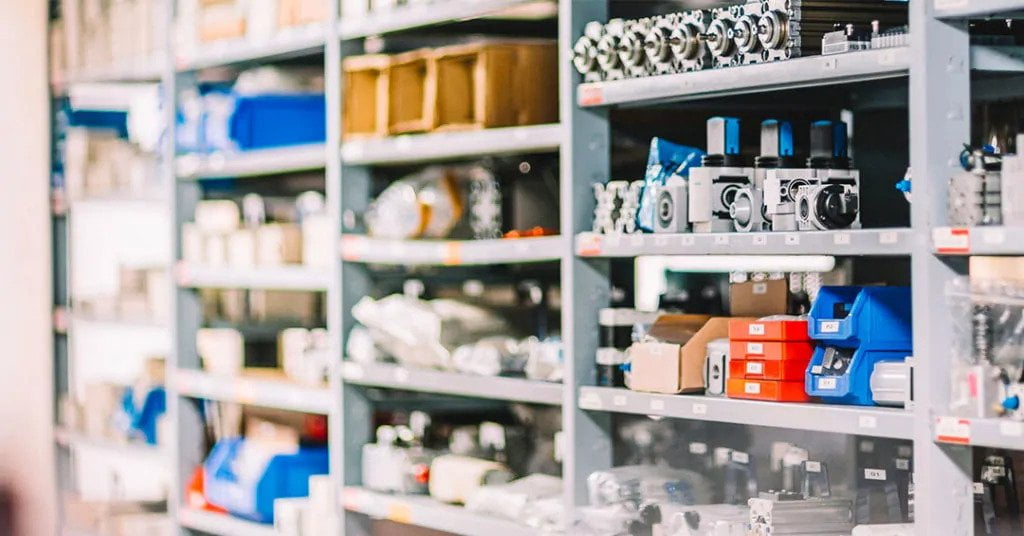
Spare parts management is a huge priority for any business that relies on being able to find the correct part at a moment’s notice. But you also need to have a system for managing your spare part inventory systems that spans beyond simply knowing the location of a part. You also need to know how many of each type of part you have at any given time so you will know when you need to reorder specific parts.
Having an organized spare parts management system can help you find parts more efficiently, minimize production or performance disruptions and reduce or eliminate expedited shipping costs. Keep reading to find out some helpful tips for spare parts management.
1. Plan Ahead
Instead of waiting until something happens, and you need a part or more than one of the same part, plan ahead and buy several spares. This will help you prevent problems before they can happen. If you find that the parts you need are often out of stock, it’s important to forecast your demand for those parts. Determine why you need those particular parts so often. Then, order several spares accordingly. For example, if you know you often have issues with optical sensors, you may want to buy in bulk to save money.
Of course, this won’t be cost-efficient for parts that are extremely expensive. But if you’re having frequent failures on an expensive part that don’t make sense, it could be stemming from a whole different issue. For example, it may be time to consider an alternative model or make of equipment to combat that issue.
2. Implement an Inventory Control System
An inventory control system can help you efficiently track how often you are using a part and whether a part needs to be reordered. If you have the time, you can create and implement your own inventory control system. If not, there are several ready-made programs you can purchase to help you manage your inventory. If you run a small operation, you can likely do it yourself without having to purchase an expensive software program.
You also need to have a designated storage space for inventory with a door that you can lock. If your inventory storage is not secure, parts can be removed and replaced at-will without the opportunity for you to confirm that proper recordkeeping is taking place.
3. Know Lead Times
A key element to any successful spare parts management program is knowing and understanding lead times. If your company can afford to have downtime while you wait on a part, then it won’t be as critical to focus on this. But, if you rely on production and performance times, then you’ll definitely need to research how long it will take to get a particular part when you need it right away. You may also want to investigate off-brand parts (if they are appropriate to use) to see if they can be delivered more quickly.
4. Replace Parts Immediately
Don’t wait. Once a part is pulled from inventory, put in an order to replace it. Otherwise you may forget. As long as you have an efficient inventory control system in place, you shouldn’t have any issues with replacing parts immediately.
5. Never Assume You Won’t Need Parts
Even if you just started your operation or just had new equipment installed, never assume that you won’t need parts. Add any new parts that are critical or that you think you will likely need to your inventory as soon as possible. Then, you won’t have to suffer downtime if something malfunctions or breaks. If you’re unsure of what you might need, check with the equipment vendor for spare part recommendations. Then, decide which ones you want to order more than one of, depending on cost and length of shipping time.
6. Have the Right Tools for the Job
And last but not least, invest in the right tools for the job. For example, you’ll benefit from a highly efficient laptop with at least a i7 quad-core processor with 16 GB RAM so you can quickly check your inventory and order new parts as needed. You’ll also want to invest in shelving and bins to keep spare parts in, as well as a label maker to label parts at their locations and order numbers.
Talk to other people who have successfully implemented their own spare parts management/inventory control program to get additional ideas about products and tools you may want to invest in.